OEM High Performance Torsional Vibration Dampers
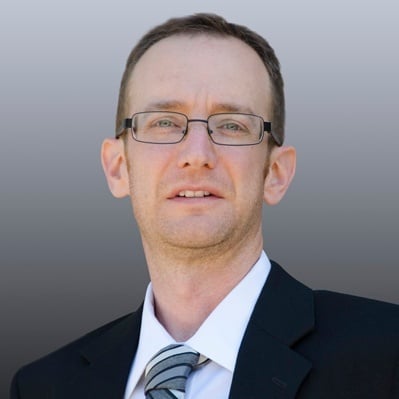
Torsional Vibration Damper Introduction
The engineering challenges of developing an OEM high performance engine are increasingly complex. Design requirements include generating more power from a smaller displacement, combined with airflow restrictions under the hood, while meeting long life durability.
All three are intertwined with controlling crankshaft torsional vibration. This back-and-forth oscillation of the crankshaft along its rotational axis is due to combustion forces. It is particularly critical at engine speeds where resonance can amplify the torsional amplitude forces. If left unchecked, torsional vibration contributes to engine failure.
A torsional vibration damper (tvd) is used on the snout of the crankshaft to control this force. A viscous type damper is often preferred in high performance applications for its superior durability and broad frequency range damping characteristics. Key is its ability to transform torsional vibration to heat and dissipate it through the damper housing.
In this article we’ll take a look at how modern advances in Vibratech TVD viscous dampers are helping engine designers overcome these modern challenges and push performance to new levels.
About Vibratech TVD
Vibratech TVD (formerly Houdaille) invented the torsional viscous damper in 1946. Headquartered today in Springville, New York, the company is an award winning supplier and currently serves over 25 OEM accounts. These include global brands in automotive high performance, off-highway, railroad, marine, stationary power, public transit, and defense. Vibratech TVD is ISO 9001:2015 Design and Development, and Quality Systems certified.
Vibratech TVD’s engineering and manufacturing capabilities include:
- Torsional vibration analysis and modeling.
- Torsional vibration damper development.
- Low-to-high volume manufacturing.
- Precision CNC machined components.
- Laser welding. Steel and aluminum.
- Precision silicone injection metering.
- Data matrix serialization and laser engraving.
- Global logistics fulfillment.
Let’s look at the basics to understand the advancements. A Vibratech TVD viscous damper is designed from three main components; an inertia ring, silicone fluid, and housing. It is commonly mounted to the crankshaft with a press fit hub or flange. As the crankshaft twists and rebounds during combustion, the oscillation between the housing and inertia ring transforms vibration energy to heat by sheering through the silicone. The heat then radiates out the housing.
Challenge 1:
Increasing power per cylinder.
To meet environmental regulations and material reduction, plus maintaining acceptable power output for the consumer is a challenge. Downsizing the engine and increasing power per cylinder is often accomplished by introducing forced induction. This results in higher combustion pressure and more force applied to the crankshaft. Torsional vibration amplitude increases and the viscous damper works harder to remove it. Subsequently the damper generates more heat.
In addition, horsepower is a function of revolutions per minute (RPM). As the engine fires faster and faster, RPM determines the frequency of torsional vibration. The result is a wide frequency range of harmonics. It is necessary to avoid resonance with the rotating assembly’s natural frequency. If this can not be avoided, the resulting amplitude spike must be diminished with optimum damping to protect from catastrophic engine failure.
New innovations in Vibratech TVD viscous dampers make it possible to maintain optimum heat dissipation and protect across a broader range under these challenges.
Nested - Vibratech TVD torsional vibration damper
In a Vibratech TVD nested viscous damper design, two independent inertia rings are contained within the housing. Each inertia ring is constructed from different materials to provide unique damping characteristics. For example, iron and bronze. The multi-mode effect broadens RPM range effectiveness for today’s high revving performance engines. It also helps to reduce harsh vibrations off-resonance. It’s ideal for new engines with smaller displacement and higher power output.
Dual Mode - Vibratech TVD Torsional Vibration Damper
Dual Mode – Vibratech TVD’s dual mode viscous damper design splits the outer housing into two separate chambers. Each chamber can contain different inertia ring materials and silicone viscosities to achieve desired damping. Furthermore, twice the heat dissipation can be achieved by machining cooling channels into the housing on both sides. It’s ideal for high-end automotive performance in excess of 250 horsepower per liter.
“The use of split inertia ring chambers, to help divide up the thermal dissipation, has been the most impactful innovation,” comments Vibratech TVD Product Engineering Manager / Sr. Product Engineer, Aaron Neyman. “We’ve used them as OEM on many high performance forced induction applications.”
Case Use - V8 American Muscle
A Detroit based automotive OEM was developing a limited-edition model. Powering it would be a 6.2L V8 equipped with a 3.0L supercharger and modified to be their most powerful internal combustion engine ever to hit showroom floors. Published specs were 1,025HP and 945 lb-ft of torque on E85. Cylinder pressure was pushed higher than previous iterations and concerns rose that using their current OEM elastomer damper would become a problem.
The OEM partnered with Vibratech TVD to develop a better solution. A nested viscous damper was co-designed. Both peak torsional vibration and off resonance vibration were greatly diminished across the RPM range by utilizing two different inertia ring materials inside the housing. The damper also features a bolt on one-piece, black anodized aluminum pulley designed to pull away excessive heat, drive components, and maintain envelope space. The pulley design integrates both a 10 rib supercharger and 6 rib accessory drive.
To meet OEM quality and delivery requirements, each damper component was precision machined in Vibratech TVD’s high speed CNC machining center with integrated CMM for statistical process control. Then assembled on a semi-automated line featuring laser welding with leak down testing and precision metered silicone injection. Finally the damper was laser engraved with Vibratech TVD’s performance aftermarket and racing division’s brand logo; Fluidampr. A brand well respected and acclaimed amongst professional race engine builders.
Challenge 2:
Restrictive under hood airflow.
The heat generated by a viscous damper has to go somewhere. Especially as it works harder with increased power per cylinder. The challenge is that engine bays are getting more crowded. Ambient airflow more restrictive.
The silicone used in a Vibratech TVD viscous damper already has a superior advantage of maintaining optimum viscosity across a wide temperature range. It is very thermally stable compared to other damping mediums. Preserving that integrity depends on adequate heat dissipation.
There are several methods Vibratech TVD can employ with viscous damper design itself.
Materials
Aluminum provides greater heat dissipation than steel. In many high performance race applications, the accessory drive pulley(s) are constructed from aluminum to draw heat away from a steel outer housing.
In OEM high performance the outer housing can also be constructed from aluminum. It can then be mounted to a steel crankshaft hub for durability. The extra benefit of lighter weight also helps the engine accelerate quicker through the RPM range.
Cooling Fins
Cooling fins machined into the outer housing increase the surface cooling area.
Coatings
Vibratech TVD utilizes a variety of non-insulating coatings depending on the application. These provide optimum heat dissipation and also corrosion protection.
Dual Mode
In a Vibratech TVD dual mode viscous damper, both outer housing chambers can contain multiple cooling channels. With this design twice the heat dissipation is achieved. The method is also ideal for extreme off-highway applications with both high heat and high vibration amplitude.
Active cooling
When ambient air cooling is not adequate, then active cooling becomes a viable Vibratech TVD option. With the inertia ring and silicone damping medium already contained in a sealed housing, it’s feasible in a clean sheet design to enclose the damper behind the timing cover. The engine’s oiling system sprays into a specially designed outer housing channel. The oil absorbs the heat and exits the channel. It returns to the pan by way of the timing component routing. This option from Vibratech TVD was deployed on an OEM hypercar partnering with a world renowned race engine manufacturer.
Challenge 3:
Long product life.
Engine durability is essential to maintain productivity. Especially in industries critical to flow the economy, such as off-highway, transportation and marine. Downtime costs vary widely and can be detrimental to operations. Vibratech TVD works with OEMs to develop a torsional vibration damper to meet durability as required in its environment. This has included numerous extreme condition testing with United States military.
Quality control
Vibratech TVD is ISO 9001:2015 quality systems certified. As such, silicone is sampled and regulated internally to ensure proper proprietary specifications. By doing so, damper wear can be determined per design application.
Proprietary internal bearings
Vibratech TVD develops its own low friction proprietary internal bearings. The design combines both radial and thrust movement with minimal wear. Making the bearings ideal for extreme conditions and overall superior viscous damper durability.
Corrosion resistant coating
The most popular Vibratech TVD viscous damper finishes are RoHS compliant black zinc plating for steel and clear coat anodize for aluminum.
Case Use - Hybrid Electric Powertrain
Passenger comfort is important to transit bus operators. In one instance, an OEM manufacturer was challenged by their customer with finding a noise, vibration and harshness (NVH) solution that would be acceptable. The issue held up delivery of approximately 150 transit buses and millions in revenue.
The powertrain consisted of a diesel engine mated to an electric hybrid transmission. At low speed, driveline vibration resonance with the floor panels created uncomfortable NVH.
The transit bus manufacturer in-turn partnered with Vibratech TVD to address the issue at the source. The request was to develop a highly durable torsional damper to install in the driveline. To shorten development time and resolve the end-client’s concerns quickly, Vibratech TVD pulled in their cross-industry experience in extreme climate, over-the-road truck and military viscous damper development. A current Vibratech TVD extreme-duty viscous damper matched the damping properties. The solution was as simple as mounting it to the engine’s output flange with an adapter.
The adapter was developed within Vibratech TVD’s engineering and manufacturing facility. Then it was fitted to a prototype for installation and mobile torsional vibration analysis tested. Success.
With NVH resolved to the end-client’s complete satisfaction, Vibratech TVD transitioned to production and delivery. Within weeks the manufacturer had all transit buses in waiting updated, and moved to include the new Vibratech TVD driveline damper in their future builds.
In this case, an OEM high performance viscous damper technology developed for extreme conditions and military use benefited reduced emissions public transportation.
Conclusion
Designing an OEM high performance engine is no easy task. Constraints and regulations are leading to remarkable innovations and power in a smaller displacement. As a result, higher cylinder pressure and a wider RPM range are putting more importance on the torsional vibration damper.
Vibratech TVD brings over 75 years of torsional vibration analysis experience and leads the way in new viscous dampers that excel in these challenges. Design variations, material composition, and numerous cooling capabilities all contribute to delivering a long lasting, superior product. Award-winning precision manufacturing, located in the United States, offers the reliable assurance OEMs require.
“The best time to make space for a torsional vibration damper is right away if you’re doing a clean sheet design,” concludes Neyman. “You can always give space back. Next, an in-depth torsional assessment is recommended once a rotating assembly is designed to determine resonance within the operating range.”
Make Vibratech TVD your engine development partner. Call (716) 592-1000 or contact us for consultation.